1氨氣供應不足
氨氣供應不足主要體現(xiàn)在SCR反應區(qū)需要的氨氣量得不到足夠的供應,在供氨系統(tǒng)無外漏的情況下,造成該故障的主要原因為供氨系統(tǒng)壓力低及供氨管路系統(tǒng)不暢通,因此應從氨站內(nèi)氨氣制備系統(tǒng)和供氨管路系統(tǒng)進行故障分析。
1.1液氨蒸發(fā)器出力不足
由圖1可知,該脫硝氨氣制備系統(tǒng)簡單,在液氨儲罐液位正常情況下,供氨壓力與液氨蒸發(fā)器出力相關(guān)。當鍋爐噴氨量增大或液氨蒸發(fā)器加熱蒸汽參數(shù)(設(shè)計加熱蒸汽壓力為0.15MPa,溫度為170℃)下降時,液氨蒸發(fā)出的氨氣降低,造成供氨壓力下降。該公司SCR反應器設(shè)計有供氨壓力低自動退出的保護。當氣溫低于-7℃時,蒸發(fā)器入口蒸汽壓力不足0.1MPa,溫度僅110℃左右,已接近飽和蒸汽參數(shù),無法滿足蒸發(fā)器需求,導致供氨壓力低,脫硝退出。
經(jīng)檢查有以下問題:
(1)鍋爐輔汽到氨站加熱管道過長,管道壓損大,約為0.5MPa;
(2)沿程管路保溫效果不好,溫降大,約為180K;
(3)沿程疏水閥開度過小,不能將管路的新生凝結(jié)水疏盡;
(4)氨站蒸發(fā)器間歇性用汽;
(5)氨站用汽為該路汽源的末端用戶;
(6)輔汽聯(lián)箱汽源為四抽供汽,滑壓運行,機組負荷低時輔汽聯(lián)箱壓力低。
蒸發(fā)器加熱蒸汽設(shè)計為鍋爐輔助蒸汽,且溫度不低于200℃,而實際僅為110℃左右,無法滿足蒸發(fā)器對蒸汽的設(shè)計參數(shù)要求。經(jīng)綜合分析得出加熱蒸汽品質(zhì)低是導致蒸發(fā)器出力不足的主要原因。
為防止反應區(qū)供氨不足,主要采取了以下措施:
(1)將冷再至輔汽聯(lián)箱壓力投自動,防止機組負荷低造成氨站加熱蒸汽壓力過低;
(2)將沿程管路疏水微開,確保管道無積水;
(3)在分布式控制系統(tǒng)(DCS)中增加氨站加熱蒸汽溫度和壓力低報警?,F(xiàn)即使大氣溫度低于-10℃,且機組負荷低于500MW時,蒸發(fā)器入口蒸汽溫度基本在220℃以上,壓力均在0.3MPa以上,蒸發(fā)器熱媒溫度能穩(wěn)定在70~80℃,完全達到運行要求。
1.2氨氣管道堵塞
機組在緩沖罐出口氨氣壓力和溫度均正常的情況下,SCR反應區(qū)氨氣流量在供氨調(diào)節(jié)閥全開后仍然偏低。為防止脫硝超標,采用提高供氨壓力、改善入爐煤煤質(zhì)、改變磨煤機組組合、運行調(diào)整等輔助手段降低SCR反應器入口NOx質(zhì)量濃度以減少噴氨量。
為排查原因,利用氨氣檢漏儀對供氨管路系統(tǒng)進行檢測排查,均未發(fā)現(xiàn)氨氣外漏現(xiàn)象。經(jīng)熱控及機務(wù)現(xiàn)場試驗,判斷供氨管路系統(tǒng)各閥門閥芯無脫落。在脫硝系統(tǒng)停運隔離且已被氮氣置換后,對阻火器進行解體檢查,發(fā)現(xiàn)阻火器堵塞嚴重,對阻火器中結(jié)垢物質(zhì)進行化驗,其主要成分為Fe2O3及SiO2。
為防止阻火器再次堵塞,在阻火器安裝前,對供氨管路系統(tǒng)進行徹底吹掃。濾網(wǎng)及阻火器清堵完成、管道吹掃完畢后(清堵后的阻火器見圖1),恢復系統(tǒng),氨氣流量明顯增大?,F(xiàn)將阻火器、供氨管道積灰檢查納入機組檢修時必檢項目。采取上述整改措施后,脫硝系統(tǒng)運行了約一年半時間,氨氣供應穩(wěn)定,滿足全負荷下脫硝系統(tǒng)運行要求。
圖1 清理后的阻火器
2氨稀釋風量低
氨氣噴入SCR反應器之前,為保證氨空比低于8%,要充分利用空氣進行稀釋。如果氨稀釋風量低,會影響噴氨量的增加。SCR反應器入口NOx質(zhì)量濃度高時,為保證煙囪入口NOx質(zhì)量濃度不超標,增加噴氨量,由于氨空比的限制,噴氨增加量就會受到限制。
氨稀釋風體積流量降低到一定程度時,噴氨量不能保證脫硝的全負荷運行。在氧量充足的條件下,熱力型NOx生成主要受爐內(nèi)溫度制約,燃料型NOx則取決于HCN、NH3等中間產(chǎn)物的生成率,而生成率也是受爐內(nèi)溫度的制約。為查找該公司氨稀釋風體積流量低于設(shè)計值(9000m3/h)的原因,機組運行中分別對風機入口濾網(wǎng)、風機性能、風機出口自動切換擋板、氨稀釋風管道等進行排查,均未發(fā)現(xiàn)明顯異常。
機組停運后,經(jīng)對氨稀釋風系統(tǒng)設(shè)備及管道排查后發(fā)現(xiàn):
(1)氨空混合器后的母管內(nèi)積灰嚴重,圓形的分配器的截面積堵塞近50%;
(2)噴氨支管流量縮孔堵塞,部分被積灰堵死。
待積灰清除后,氨稀釋風量大大增加。如6號鍋爐在清理積灰前氨稀釋風體積流量為6448m3/h,積灰清理后氨稀釋風體積流量增加到9493m3/h,且已超過變送器量程。由此可知,氨空混合器后的氨氣分配器和噴氨支管流量縮孔堵塞是造成氨稀釋風量低的主要原因。
為防止類似故障發(fā)生,采取了如下防堵措施:
(1)將氨空混合器后的母管和噴氨支管流量縮孔列入機組每次檢修的必檢項目;
(2)提高氨氣純度,不定期抽檢,減少氨氣的雜質(zhì)攜帶;
(3)在稀釋風機入口加設(shè)了一道致密的濾網(wǎng),并由檢修人員定期清灰。自防范措施實施后,2臺氨稀釋風機運行時氨稀釋風體積流量均能保持在9000m3/h以上。
3噴氨自動控制效果差
鑒于噴氨控制系統(tǒng)的大滯后特性,SCR脫硝噴氨自動控制系統(tǒng)不能簡單地將煙囪入口NOx質(zhì)量濃度作為被調(diào)量,否則噴氨自動投入后系統(tǒng)始終在反復振蕩。負荷變化、燃燒狀況變化也會造成SCR反應器入口NOx質(zhì)量濃度大幅變化。SCR反應器入口NOx質(zhì)量濃度變化引起SCR脫硝噴氨調(diào)節(jié)閥無法立即動作,噴氨調(diào)節(jié)閥過調(diào)量較大,最終造成煙囪入口NOx質(zhì)量濃度時有超標情況出現(xiàn)。
合理的SCR噴氨調(diào)節(jié)閥控制邏輯應以煙囪入口NOx質(zhì)量濃度為控制目標,以SCR反應器出口NOx質(zhì)量濃度為中間控制對象,以噴氨量為主要調(diào)節(jié)回路,同時增加調(diào)節(jié)前饋。基于此,將原噴氨自動控制邏輯修改為帶前饋的回路控制系統(tǒng)(見圖5)。
鍋爐總風量經(jīng)過函數(shù)f4(x)得出噴氨量前饋值。SCR出口和煙囪入口NOx質(zhì)量濃度實際值經(jīng)過微分函數(shù)f1(x)、f2(x)、f3(x)得出煙囪入口NOx質(zhì)量濃度預測值,該預測值再和煙囪入口NOx設(shè)定值相比較,利用PID調(diào)節(jié)器1得出SCR反應器出口NOx質(zhì)量濃度的中間值,SCR反應器出口NOx質(zhì)量濃度的中間值再和SCR反應器出口NOx質(zhì)量濃度實際值相比較,利用PID調(diào)節(jié)器2得出噴氨量。
該噴氨量與噴氨量前饋值之和得出噴氨量設(shè)定值。噴氨量設(shè)定值再與噴氨量實際值相比較,利用PID調(diào)節(jié)器3得出噴氨調(diào)節(jié)閥的調(diào)整指令。該調(diào)節(jié)回路提高系統(tǒng)的響應速度和精確度;同時,充分引入鍋爐總風量的前饋量,使噴氨自動控制系統(tǒng)在機組升降負荷、煤質(zhì)變動情況下均能保持良好的跟隨性。
噴氨自動控制優(yōu)化后,機組在50%~100%負荷率下能保持自動投入。正常工況下煙囪入口NOx質(zhì)量濃度均能控制在設(shè)定值(50mg/m3)內(nèi),穩(wěn)態(tài)條件下能控制在設(shè)定值±5mg/m3以內(nèi),自動控制效果良好。
研究結(jié)果表明:優(yōu)化脫硝噴氨自動控制邏輯,既可以提高煙囪入口NOx質(zhì)量濃度控制精確度,又可以有效降低脫硝系統(tǒng)還原劑耗量,對于提高脫硝系統(tǒng)運行的經(jīng)濟性和安全性都具有重要意義。
圖2 新噴氨調(diào)節(jié)閥控制邏輯
4噴氨均勻性差
隨著SCR脫硝系統(tǒng)運行時間的延長,SCR脫硝系統(tǒng)出現(xiàn)故障,氨逃逸率有增大趨勢。SCR反應器出口氨逃逸體積分數(shù)逐漸增加,從早期不足3×10-6(設(shè)計值小于3×10-6)升高到42×10-6。較高的氨逃逸體積分數(shù)對SCR反應器、空氣預熱器、低溫省煤器等設(shè)備構(gòu)成嚴重威脅。
按照催化劑設(shè)計壽命、取樣分析及使用情況,催化劑失效可能性不大。催化劑磨損會造成氨逃逸率增加,脫硝系統(tǒng)氨氣噴嘴堵塞將加劇氨逃逸。催化劑及噴嘴磨損情況只能在機組停運后檢查確認。為查找噴氨系統(tǒng)故障,采用排除法,首先從容易判斷的噴氨均勻性著手試驗分析。
氨逃逸率與氨與NOx的混合效果有著密切的關(guān)聯(lián),氨的分布對SCR脫硝系統(tǒng)運行的最佳性能非常重要。根據(jù)噴氨均勻性試驗結(jié)果分析,可以看出SCR反應器入口截面NOx質(zhì)量濃度分布偏差較小,最大為352.7mg/m3,最小為267.6mg/m3,分布較為均勻(見表1)。
表1 滿負荷工況下SCR反應器入口截面NOx質(zhì)量濃度分布 mg/m3
SCR反應器出口截面NOx質(zhì)量濃度沿寬度方向均呈階梯形分布:靠反應器中心線區(qū)域NOx質(zhì)量濃度偏高,靠反應器外側(cè)墻區(qū)域NOx質(zhì)量濃度偏低,見表2。
表2 滿負荷工況下SCR反應器出口截面NOx質(zhì)量濃度分布 mg/m3
SCR反應器出口NOx質(zhì)量濃度分布偏差較大,存在大面積NOx質(zhì)量濃度顯著較高的點。與此相對應,反應器左后區(qū)域氨逃逸體積分數(shù)均超過67.5×10-6,右后區(qū)域氨逃逸體積分數(shù)均超過75.4×10-6。氨逃逸在線監(jiān)測儀表安裝于反應器靠右側(cè)墻上,這也解釋其顯示值較高的原因。
通過現(xiàn)場分析發(fā)現(xiàn)反應器中間靠前區(qū)域的噴氨支管U形管有7根被堵死(存有大量積水),這些管道對應的噴氨區(qū)域無氨氣噴入,造成該區(qū)域出口的NOx質(zhì)量濃度較大。由于氨氣都噴入反應器左后和右后區(qū)域,造成這些區(qū)域NOx質(zhì)量濃度較小,甚至測量不到NOx質(zhì)量濃度。
局部區(qū)域過量噴氨勢必造成局部區(qū)域氨逃逸體積分數(shù)較大。支管疏通后,在線噴氨量顯著下降,由此可以得出,噴氨支管堵塞是導致噴氨量較大和噴氨不均勻的主要原因,但經(jīng)測量SCR反應器出口氨逃逸體積分數(shù)后發(fā)現(xiàn)仍有部分區(qū)域氨逃逸體積分數(shù)較高情況。
根據(jù)SCR反應器出口NOx質(zhì)量濃度及逃逸氨分布情況,對噴氨格柵各支管手動閥開度進行多次調(diào)節(jié)。噴氨優(yōu)化調(diào)整后,SCR反應器出口截面NOx質(zhì)量濃度分布較均勻,見表3。
表3 滿負荷工況下SCR反應器出口截面NOx質(zhì)量濃度分布mg/m3
進入第1層催化劑前NOx與氨的混合均勻且速度分布均勻時,才能保證脫硝效率和出口氨逃逸率穩(wěn)定。噴氨優(yōu)化調(diào)整后SCR反應器出口截面NOx質(zhì)量分布均勻性顯著提高。SCR反應器出口氨逃逸體積分數(shù)分布較為均勻,平均為1.31×10-6,最大為2.64×10-6,噴氨不均勻造成氨逃逸局部超標現(xiàn)象得到消除。優(yōu)化調(diào)整后反應器出口氨逃逸體積分數(shù)分布較均勻,見表4。
表4 滿負荷工況下SCR反應器出口截面(φ(O2)=6%)氨逃逸體積分數(shù)分布
與優(yōu)化調(diào)整前相比,鍋爐左后和右后區(qū)域氨逃逸體積分數(shù)峰值明顯降低,整體上氨逃逸體積分數(shù)由優(yōu)化調(diào)整前最高75.44×10-6降低至2.64×10-6。由噴氨量看,在SCR反應器入口NOx質(zhì)量濃度在300~400mg/m3且煙囪入口NOx質(zhì)量濃度為42~45mg/m3工況下,優(yōu)化調(diào)整后總噴氨量降低約15.5%。噴氨優(yōu)化調(diào)整后,SCR反應器出口截面NOx質(zhì)量濃度分布均勻性顯著提高,局部較高的氨逃逸體積分數(shù)明顯降低,減小了下游空氣預熱器硫酸氫銨堵塞風險,同時隨噴氨量的下降,系統(tǒng)運行的經(jīng)濟性也得到提高。噴氨系統(tǒng)的優(yōu)化調(diào)整,不僅能有效降低脫硝反應器出口局部較高的氨逃逸體積分數(shù),而且能有效延長催化劑的使用壽命。
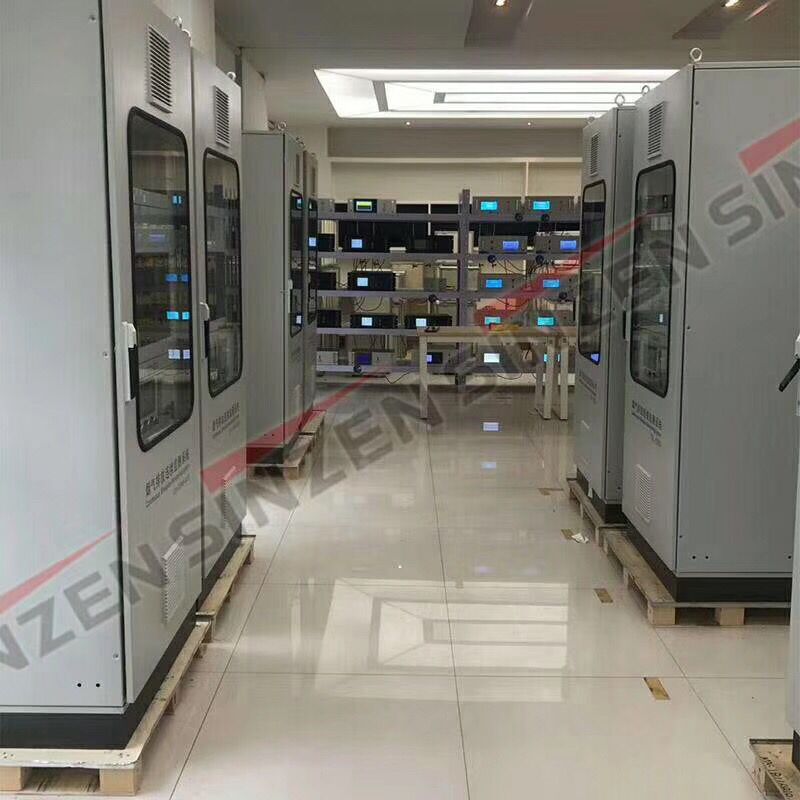